Background
Internal combustion engines are heat engines that perform the conversion of heat to mechanical energy. Internal combustion engines are very commonly used to provide mechanical energy: it is believed that there at least 1 billion internal combustion engines in the world. A large variety of internal combustion engine types exist, these types can include piston-type engines such as those used to provide mechanical energy to propel automobiles such as cars, trucks, motorcycles, busses, light aircraft, lawnmowers, and the like. Other types of internal combustion engine include types that do not have pistons, such as turbines and jet engines. Internal combustion engines can produce power in the range of a few watts to hundreds of megawatts.
In an internal combustion engine, a prepared fuel combusts with an oxidiser (often air but other sources of oxygen can be used) with the result that chemical energy stored in the fuel is transferred to the movement of an engine output (typically causing rotation of some form of drive shaft). Piston-based internal combustion engines can be produced that operate according to one of a number of different operational cycles. Among the most well-known reciprocating piston type internal combustion engine cycles are the Otto, Diesel, Brayton, Atkinson and Miller cycles. Rotary “piston” internal combustion engines can also exist and the among most well-known types is the Wankel engine (which follows approximately the Otto cycle). Turbines and jet engines (which can include turbofans, turbojets and rocket engines) are typically continuous rather than cyclical in operation.
Internal combustion engines can operate using a variety of different fuels. Examples include: petroleum oil, autogas, petrol, diesel, methane, kerosene, coal, biodiesel and hydrogen.
The performance of an internal combustion engine varies based upon factors such as energy efficiency, power to weight ratio, torque curve etc. With respect to energy efficiency, this affects the rate of recovery of usable energy from the combustion product's thermal energy. The energy can be transformed into work by utilising the increase in temperature and pressure created during combustion. The theoretical efficiency can be calculated by using an idealised thermodynamic cycle, for example, the Carnot cycle. In the Carnot cycle the efficiency depends only from high and low operating temperatures of the engine. At the present time, the maximal thermodynamic limit of efficiency for a typical internal combustion engine is understood to be about 40% for commercial Diesel engines, although laboratory tests are believed to have reached up to 49% efficiency (noting also that Otto cycle engines typically achieve thermodynamic lower efficiency than combined (Seiliger, or Trinkler, or Sabathe) cycle engines). The actual efficiency of a real internal combustion engine would be expected to be lower than such a theoretical maximum due to the impact of the real engine not benefiting from the idealised assumptions in the calculation.
Internal combustion engines produce as by-products of the combustion process air pollution emissions. These pollutants typically include CO, CO2, NOx and others. The level of pollutants produced by a given internal combustion engine will vary depending upon the fuel and combustion approach used, but also from operating parameters of the engine operating relating to the combustion process. Such operating parameters can include fuel/air ratio, operating temperature, fuel quality, etc. The typical control approach for an internal combustion engine is to monitor inputs and outputs and to vary the inputs in an effort to optimise the outputs.
Technology overview
The invention provides an engine control apparatus having a controller operable to receive input from a heat flux sensor arranged to measure combustion power within an internal combustion engine and to use said input in a control process to determine an adjustment to a controllable engine operation parameter.
Viewed from one perspective, the present teachings can provide an approach for monitoring the thermal energy produced by combustion within an internal combustion engine. Further, the present teachings can provide an approach for control of an internal combustion engine based upon the monitoring of the thermal energy produced by combustion.
Viewed from a first aspect, the present teachings can provide an engine control apparatus, comprising: a controller operable to receive input from a heterogeneous gradient heat flux sensor arranged to measure combustion power within an internal combustion engine and to use said input in a control process to determine an adjustment to a controllable engine operation parameter, further comprising the heterogeneous gradient heat flux sensor, the heterogeneous gradient heat flux sensor being arranged in direct thermal communication with a combustion chamber of the engine. By performing a direct measurement of the combustion process in this way, an engine can be controlled to provide optimised efficiency and performance.
Viewed from another aspect, the present teachings can provide a combustion system comprising: an internal combustion engine having a combustion chamber; a heterogeneous gradient heat flux sensor arranged in direct thermal communication with the combustion chamber; and an engine controller arranged to receive a signal from the heterogeneous gradient heat flux sensor and to control a controllable engine operation parameter in dependence upon said signal. Thus a combustion system can be provided that is able to operate based upon direct measurement of the combustion process occurring in the engine.
Viewed from a further aspect, the present teachings can provide a sensor kit for installation to an internal combustion engine, the kit comprising: at least one heterogeneous gradient heat flux sensor installable to be in direct thermal communication with a combustion chamber of an internal combustion engine and operable to output a signal representative of a heat flux at the sensor during a combustion cycle of the internal combustion engine, and a signal conveyor connectable to convey an output signal from the heat flux sensor to an engine management system for an engine into which the heat flux sensor is to be installed. Thereby an existing engine can be retrofitted to facilitate controllability on the basis of direct measurements of the combustion process occurring in the engine.
Viewed from another aspect, the present teachings can provide a method of controlling an internal combustion engine, the method comprising: receiving a signal from a heterogeneous gradient heat flux sensor of a combustion chamber of the internal combustion engine, wherein the heterogeneous gradient heat flux sensor is arranged in direct thermal communication with a combustion chamber of the engine; and using the signal as an input to a feedback control loop for controlling one or more controllable engine operation parameters of the internal combustion engine. Thus, an engine control approach can be adopted based upon signals collected from the combustion chamber and thus directly representative of the ongoing combustion process.
Benefits
- reduced emission
- real-time monitoring of the thermal energy produced by combustion
- optimised efficiency and performance of the engine
Applications
- Emission control in large power plant diesel and gas turbines.
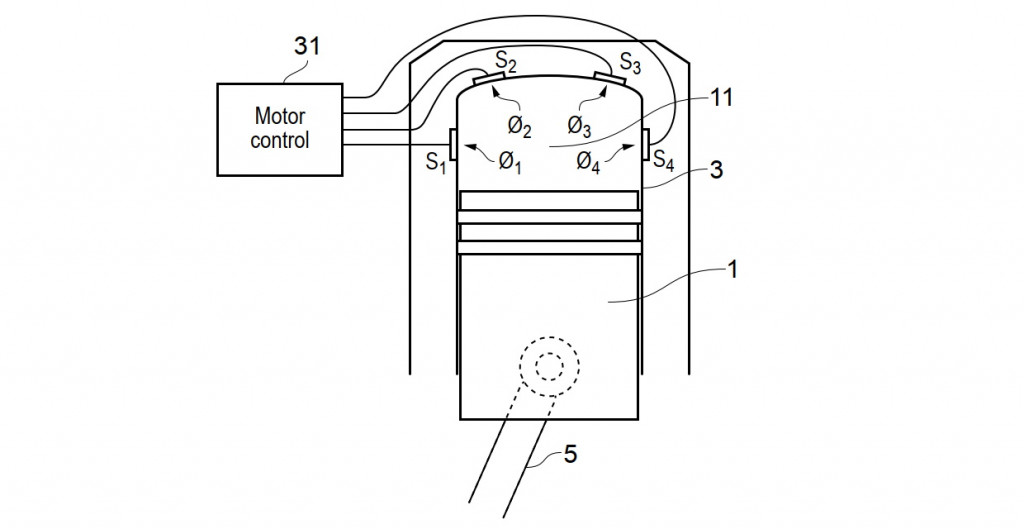
Liitteet
Lisää aiheesta
Ota yhteyttä
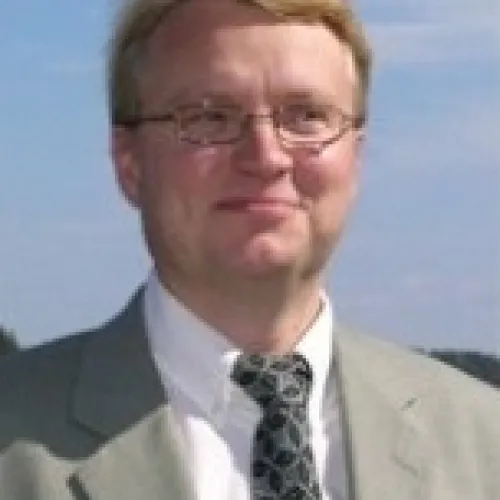
Tero Lehikoinen
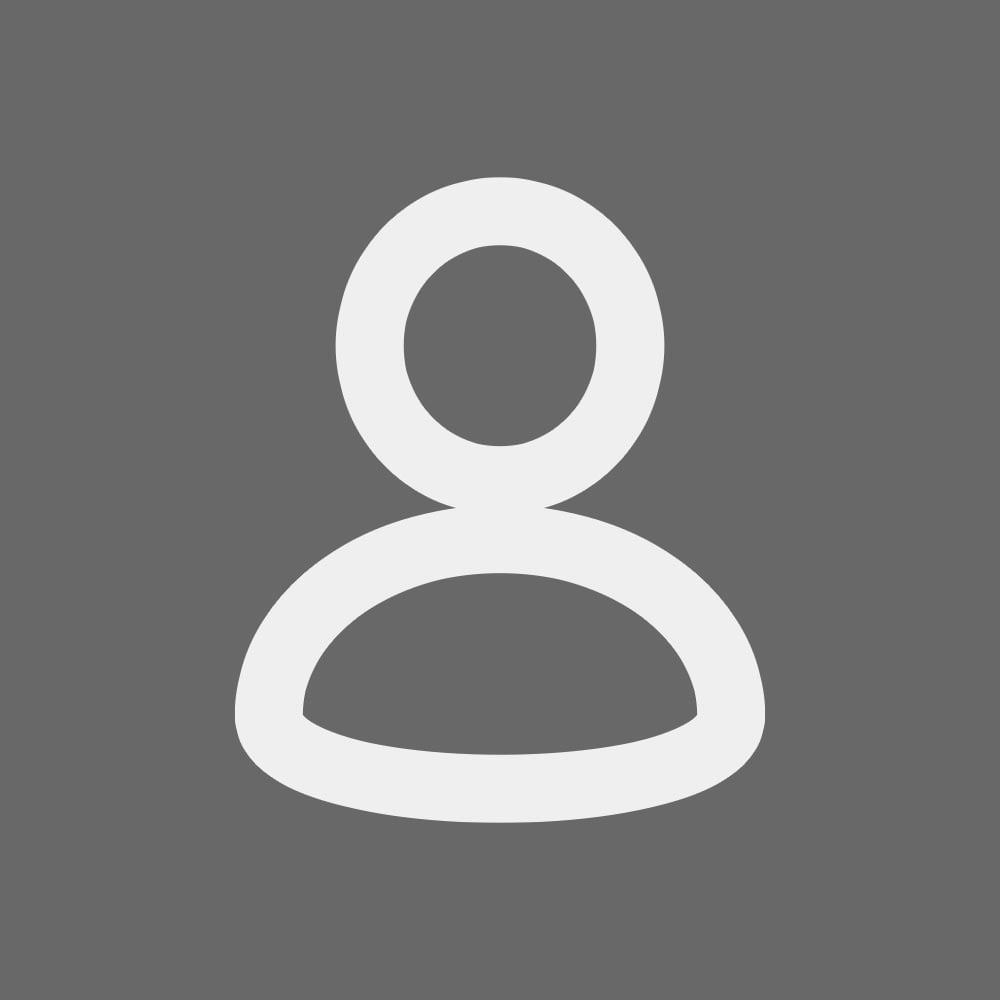