LUT University is developing digital twins to promote the growth of industrial enterprises. A digital twin may, for instance, refer to a virtual replica of a production machine. A computer-made replica can model large entities, such as a factory floor and its machinery, production processes, systems and employees.
Digital twins model machine capacities, temperatures, structural tensions and stress on wearing parts. The data from the replica can be understood at a single glance. The data shows how to increase production efficiency by, for example, adjusting utilisation rates or anticipating disturbances.
In practice, a digital twin saves time and money.
"A digital twin differs from conventional modelling in that it can be utilised at many stages of the production process. It may be used in production development, marketing, condition control, employee orientation and user training," says Aki Mikkola, LUT University's Professor of Mechanical Engineering.
A digital twin also enables the safe and cost-efficient testing of something that does not exist yet, such as planned extensions to factory buildings. Modelling shows how the production lines, employees, robots and trucks would operate in the planned space or how lost heat could be recovered into the energy system of the building.
A digital twin joins together hardware and software
Aki Mikkola and LUT University are involved in the multidisciplinary project Digibuzz, which aims to determine the best digital twin and modelling solutions for industry partners. The project examines what novel business models can be based on digital twins and how.
One of the project partners is Process Genius, a company providing industrial enterprises with online application solutions. CEO Jani Akkila says that the company's goal in the Digibuzz project is to develop its own digital twin platform that will enable the creation, productisation and global marketing of new business models.
"For example, with Raute – another company involved in the project – we could create a package that provides customers with manufacturing equipment accompanied by its digital twin. Collaboration would optimise and raise the service level of both companies," Akkila outlines.
According to LUT's Senior Researcher Juhani Ukko, leasing the capacities of manufacturing machines or selling maintenance packages could be new types of services targeted for industry.
"Factory owners have previously had to ponder which updates and maintenance services are actually necessary. Modelling would show which parts should be dealt with and in what order for the production to remain efficient," Ukko explains.
Digital twins can promote the operational autonomy of a company. They also conserve energy, nature, and raw materials. By monitoring production line components in real time, digital twins could also influence the unit prices of food products.
"Meanwhile, we can influence how costs and profits are distributed among partners in the production chain," Ukko states.
According to Jani Akkila of Process Genius, the utilisation of these new digital opportunities requires no new skills from companies.
"All companies need are experts in their own field who know their factory and equipment and know what aspects would be the most beneficial to monitor digitally," Akkila concludes.
Digibuzz
- The Digibuzz project is conducted on LUT University's multidisciplinary SIM platform. The project includes Hannu Rantanen's performance management, Lea Hannola's innovation management, Aki Mikkola's virtual design, Jussi Sopanen's machine dynamics, and Heikki Handroos's intelligent machines research groups.
- The project is led by LUT University, and also the VTT Technical Research Centre of Finland Ltd is involved. The partner companies are Raute, Mevea, Eurostep, Wärtsilä Finland and Process Genius.
- DigiBuzz is part of a more extensive Digital Twin project funded by Business Finland. LUT University's share of the funding is 1.84 million euros.
- The manufacture and operation of digital twins is taught in LUT's mechanical engineering studies. The Degree Programme in Industrial Engineering and Management combines production processes, technology and business.
More information:
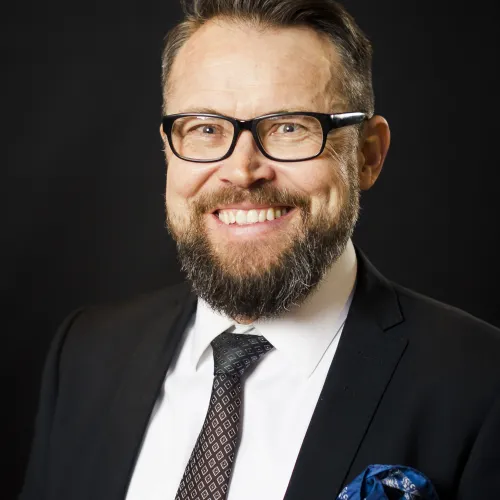
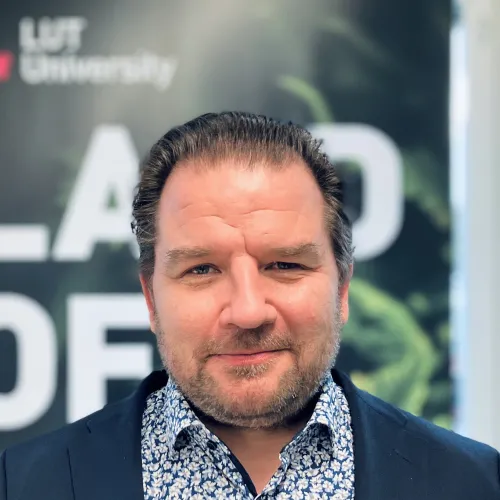