Background
In a rotating electric machine, such as an electric motor or a generator, a magnetic flux is developed between electromagnetically active parts of the rotor and the stator of the electric machine. In a radial flux electric machine, the maximum torque is proportional to the product of the air-gap radius, the area of the air-gap surface, the magnetic flux density in the air-gap, and the linear current density in the air-gap surface of the stator. Hence, without increasing the mechanical size of the electric machine, the maximum torque can be increased by increasing the linear current density because the magnetic flux density cannot be practically increased any more when the saturation point of iron has been exceeded. Increasing the linear current density increases, however, the resistive losses in the windings of the electric machine. On the other hand, the mechanical power of an electric machine can be increased by increasing the rotational speed while keeping the torque unchanged. Thus, electric machines having a high power-to-size ratio are typically high-speed machines. Increasing the rotational speed increases, however, the alternating frequency of magnetic field in a stator core structure and thereby the iron losses, i.e. the hysteresis and especially the eddy current losses, can be significant in high-speed machines. Therefore, the cooling plays a significant role in the operation of rotating electric machines.
An effective method for cooling a stator winding of an electric machine is liquid cooling where cooling liquid is in contact with, or at least in close vicinity of, electrical conductors of the winding. This invention provides a technical solutions that are suitable for arranging liquid cooling for a stator winding as well as for a stator core structure.
A simplified summary of an invention
In accordance with the invention, there is provided a new stator for an electric machine. A stator according to the invention comprises:
- a stator core structure, and
- a stator winding comprising a plurality of stator coils mechanically supported by the stator core structure.
Each of the stator coils comprises electrical conductors and a cooling tube for conducting cooling fluid in the longitudinal direction of the electrical conductors. The stator further comprises cooling elements having heat-conductive mechanical contacts with the stator core structure. The cooling elements comprise channels for conducting the cooling fluid, and the cooling tubes of the stator coils are connected to each other via the cooling elements. The above-mentioned cooling elements are capable of transferring heat caused by iron losses from the stator core structure to the cooling fluid. Furthermore, the cooling elements act as manifolds for conducting the cooling fluid between the cooling tubes of the stator coils.
In accordance with the invention, there is provided also a new electric machine. An electric machine according to the invention comprises:
- a stator according to the invention, and
- a rotor rotatably supported with respect to the stator.
An electric machine according to an exemplifying and non-limiting embodiment of the invention is a radial flux inner rotor machine where the cooling elements are placed in axial grooves on the yoke section of the stator core structure and the cooling elements comprise cooling ribs on surfaces facing away from the airgap surface of the stator core structure. The rotor may comprise e.g. blower vanes for pushing air or other gas via the airgap and/or via axial cooling channels of the rotor, and the electric machine may comprise mechanical structures for guiding the air or other gas to circulate back to the blower along the surfaces of the cooling elements that comprise the above-mentioned cooling ribs. In this exemplifying case, the cooling elements are arranged to cool not only the stator core structure but also the air or other gas that is cooling the rotor.
Attachments
Licensing contact
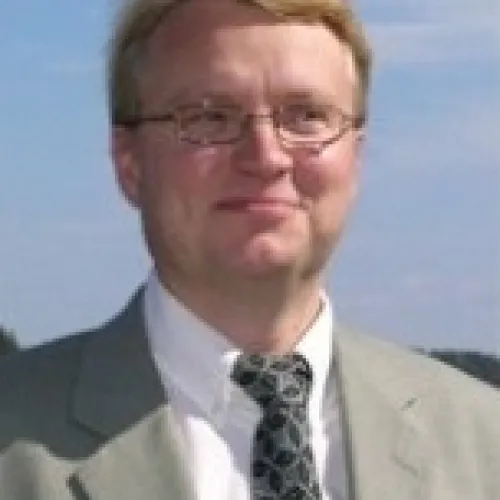
Tero Lehikoinen
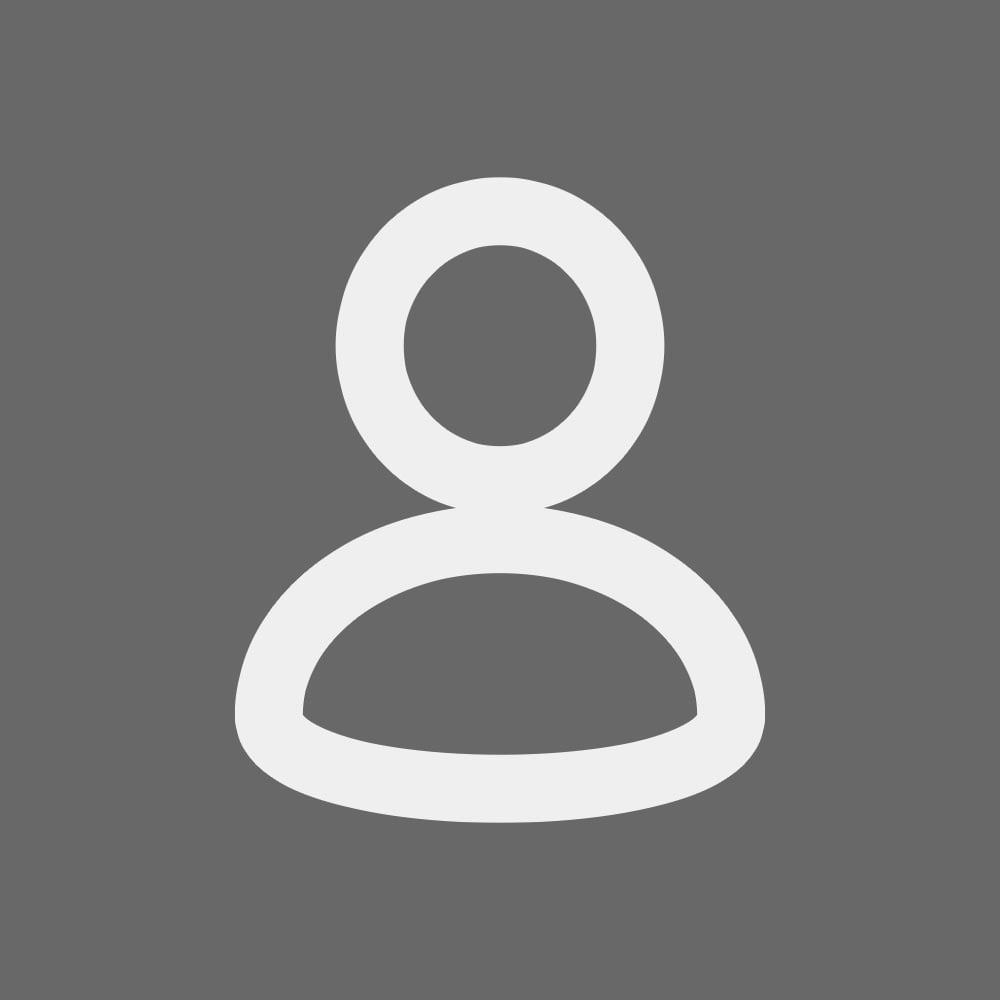