Laboratory infrastructure
The P2X Chemical Process Laboratory, a part of LUT P2X infrastructure, supports comprehensive investigations of various P2X processes under diverse conditions, facilitating both the development of novel processes and the optimization of existing ones. Equipped with state-of-the-art instrumentation, the laboratory specializes in catalyst characterization, reaction condition testing, and product analysis.
Methanol-based syntheses and Fischer-Tropsch experiments are carried out using a Micromeritics flow reactor, allowing precise control over reaction parameters and catalyst testing under various operating conditions (up to 1000°C and 100 bar). While the reactor system can operate across a wide range of temperatures and pressures, current research primarily focuses on CO- and CO2-based Fischer-Tropsch and methanol-to-olefins syntheses.
Active investigations are conducted on iron-based and cobalt-based catalysts, with efforts to optimize their formulations to enhance jet fuel selectivity while maintaining high conversion efficiency. The goal is to identify the most effective catalyst compositions for maximizing the yield of liquid hydrocarbons, including synthetic aviation fuels and lighter hydrocarbons for petrochemical applications, such as plastic production.
Membrane gas separation is utilized to selectively separate specific gases from mixtures using semi-permeable membranes. These membranes function as selective barriers, allowing certain gases to pass through while retaining others based on differences in size, solubility, and diffusion rates. This method is widely used in industries such as natural gas processing, hydrogen production, and environmental engineering for applications like carbon dioxide removal, nitrogen generation, and oxygen enrichment. It is known for its energy efficiency, modularity, and lower operational costs compared to traditional gas separation techniques like distillation and adsorption.
The dynamic adsorption setup can be used for breakthrough analysis and adsorption-desorption tests for up to 4 gases and 2 vapors, pressure 67 bar, and temperature of 180°C. There are TSA, VSA, PSA options available for swing adsorption-desorption.
For advanced analytical capabilities, the laboratory is equipped with state-of-the-art instruments, including the latest version of the Agilent 2D GC/MS chromatograph for detailed product identification and quantification, as well as an FTIR spectrometer for in situ molecular analysis. When integrated with the flow reactor, GC analysis becomes essential for precise qualitative and quantitative assessment of reaction products. Additionally, LUT facilities provide access to BET, XRD, ICP-AES, SEM, PSD, and other techniques critical for catalyst synthesis and testing.
Digital infrastructure
Beyond laboratory experiments, advanced modelling and simulation tools are employed to optimize process efficiency and support industrial-scale implementation. These tools enable the prediction of system behavior, reducing the need for extensive experimental trials.
A key focus is the development of digital twin models for critical P2X processes, allowing for the simulation of system performance under various conditions, including scale-up scenarios. A functional digital twin for methanol synthesis has already been established, with ongoing efforts to expand the scope of these models. Additionally, dynamic modeling of P2X processes under fluctuating feedstock flows is a priority. As intermittent wind and solar PV energy become more prevalent, this approach helps identify process bottlenecks and inefficiencies, leading to targeted improvements in system performance.
To support modeling, simulation, design, optimization, and control, a range of mathematical and object-based software tools are utilized:
- MATLAB and Python are used for mathematical modeling, optimization, and control, providing analytical, numerical, and statistical insights into P2X synthesis processes.
- Aspen Plus/Aspen Dynamics is employed for modeling, visualization, and simulation of both steady-state and dynamic conditions of industrial P2X units. This enables techno-economic analysis and carbon footprint assessments of industrial-scale processes.
- COMSOL Multiphysics serves as a key tool for developing digital twins of P2X processes. It enables real-time process visualization, reaction condition optimization, and predictive scaling for industrial applications.
By integrating these computational tools with experimental research, preliminary insights into P2X syntheses can be obtained before laboratory testing, and experimental results can be effectively translated beyond laboratory conditions to support industrial implementation.
Contact info
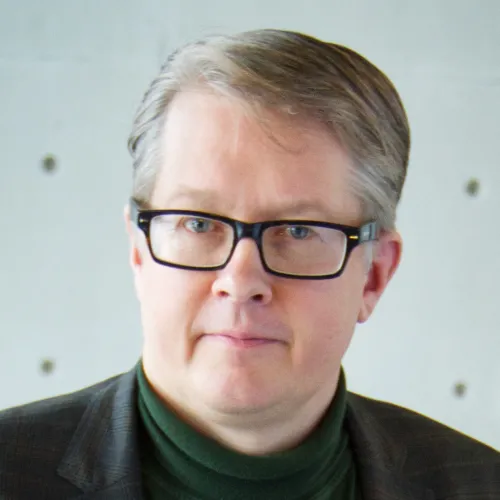
Tuomas Koiranen
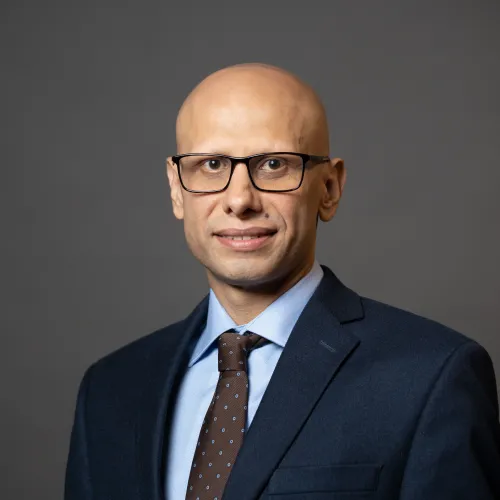