The Machine Dynamics lab at LUT University focuses on advancing the field of machine dynamics and design, with a particular emphasis on rotating machines and rotordynamics. Our research encompasses a broad spectrum of topics aimed at enhancing the performance, reliability, and efficiency of rotating machinery. Through modeling, simulation, analysis, and experimental methodologies, we strive to address critical challenges in modeling and vibration analysis, fault diagnosis, and the development of novel design strategies to improve machine lifespan and operational safety.
Our team collaborates closely with industry partners and academic peers to push beyond the state-of-the-art in machine design and dynamics, contributing valuable insights and innovations to the field. Our objective is to advance the development of modeling and experimental methodologies that facilitate the shift towards a carbon-neutral society. This involves innovating efficient solutions for energy conversion machinery, contributing significantly to sustainable solutions.
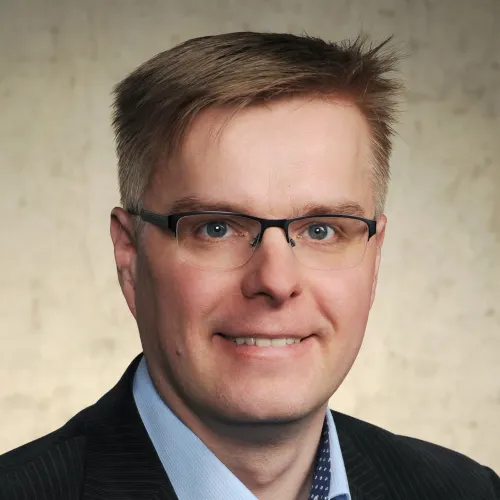
Research areas
- Rotordynamic analysis and vibration measurements
- Electromechanical analysis of mechanical systems
- Dynamic modeling of bearings and defects in mechanical systems
- Mechanical and dynamic performance analysis of electric motors
- Active magnetic bearing systems modeling and control.
- Wind turbine dynamics and permanent magnet generator analysis
- High-speed electrical machines and active magnetic bearings for compressor applications
- Real-time multibody simulation and gamification in mechanical engineering education
Infrastructure
The laboratory of machine dynamics, located at Lappeenranta campus, is equipped with several state-of-the-art device and test rigs for measurement and analysis of different phenomenon related to vibration. The experimental infrastructure supports the development of modeling methods using coding platforms such as MATLAB, Simulink, and Python, alongside finite element tools such as Ansys, ensuring robust verification of the developed methods. The infrastructure includes:
- Operational Modal Analysis (OMA) equipment and software
- Scanning Laser Doppler Vibrometer (SLVD) and single laser head
- Acoustic Camera
- Torsional Vibrometer
- Automatic Impact Hammer, manual Impact Hammer, shakers
- Piezoelectric actuator
- Accelerometers and force sensors
- Non-contact Displacement Transducers (NCDTs), rotation speed sensor
- National Instruments (NI) Data Acquisition device
Most relevant publications
Relevant projects
- High-Performance Natural-Refrigerant Compressor Technology for Industrial Heat-Pump Ecosystems (HiPerHP)
- Reluctance and Low Magnet Machine (REAL Machine)
- Development of New High Temperature Heat Pump Compressor (HTCOMP)
- EU project for the development of energy- and material-efficient drive motors (VOLTCAR)
Links
Group members
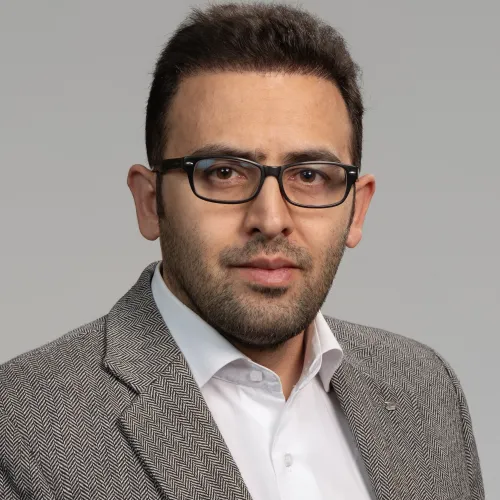
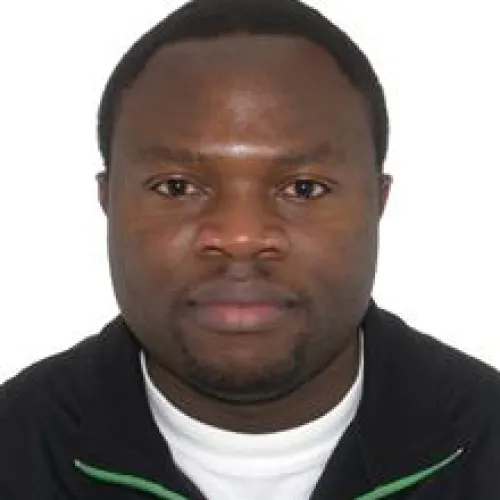
Charles Nutakor
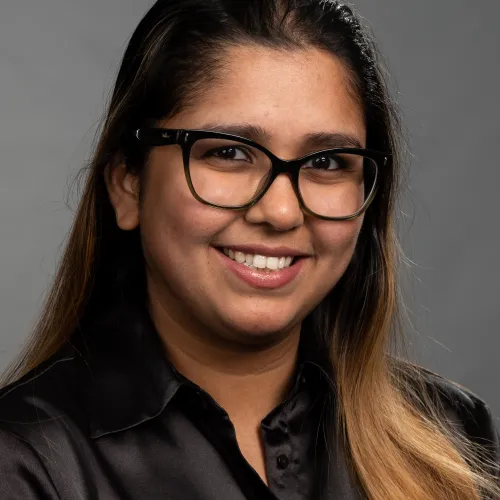
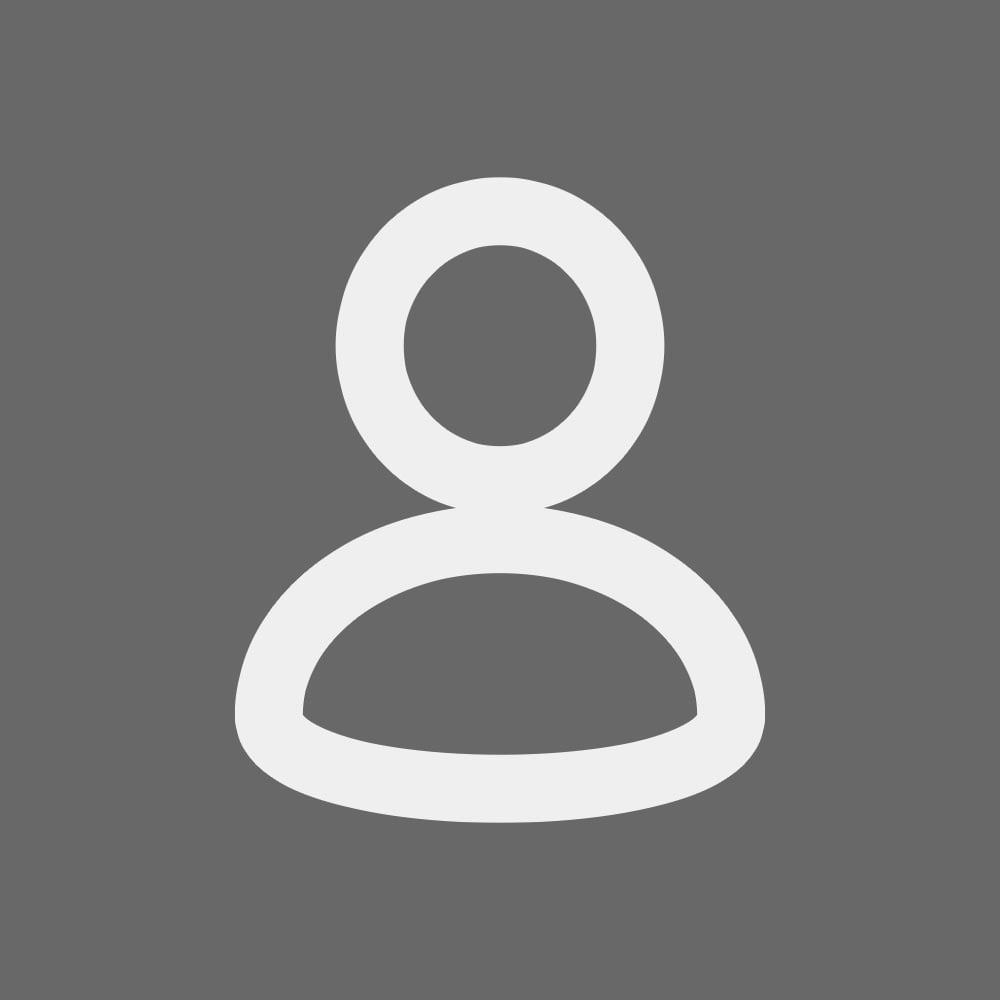
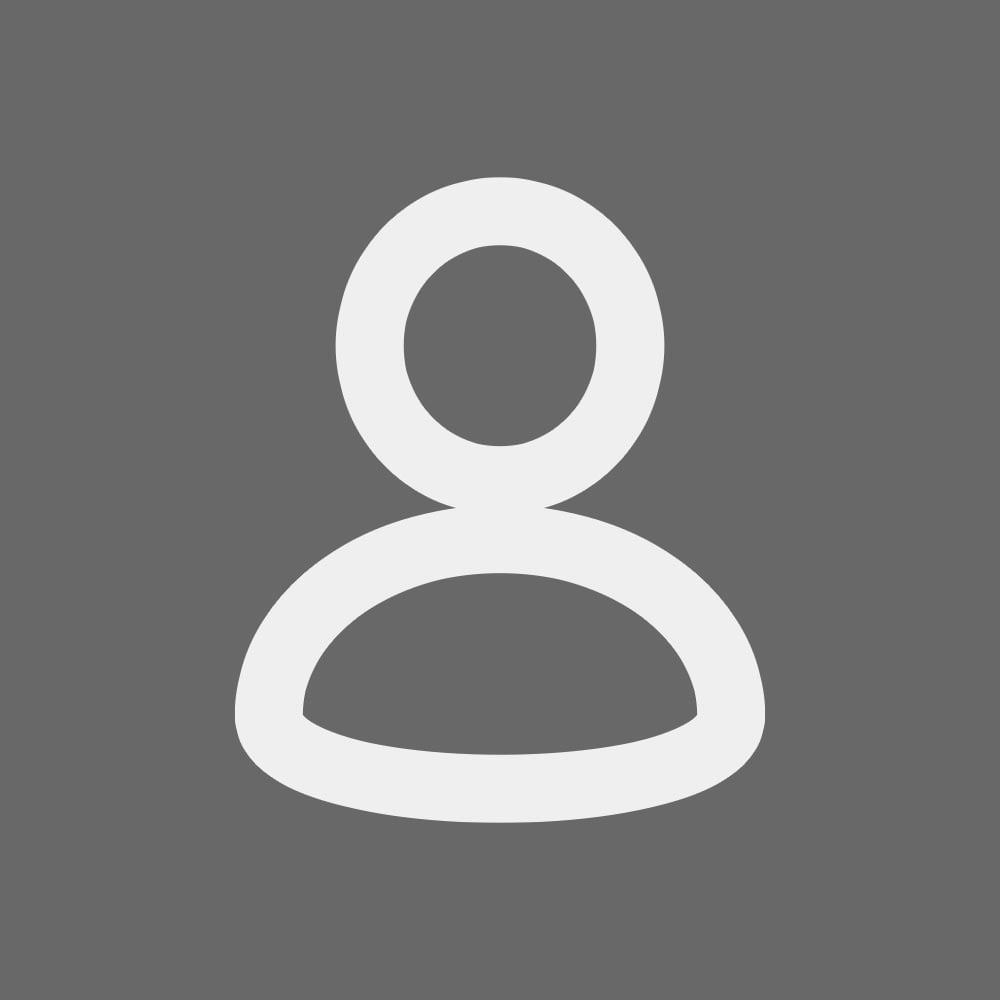
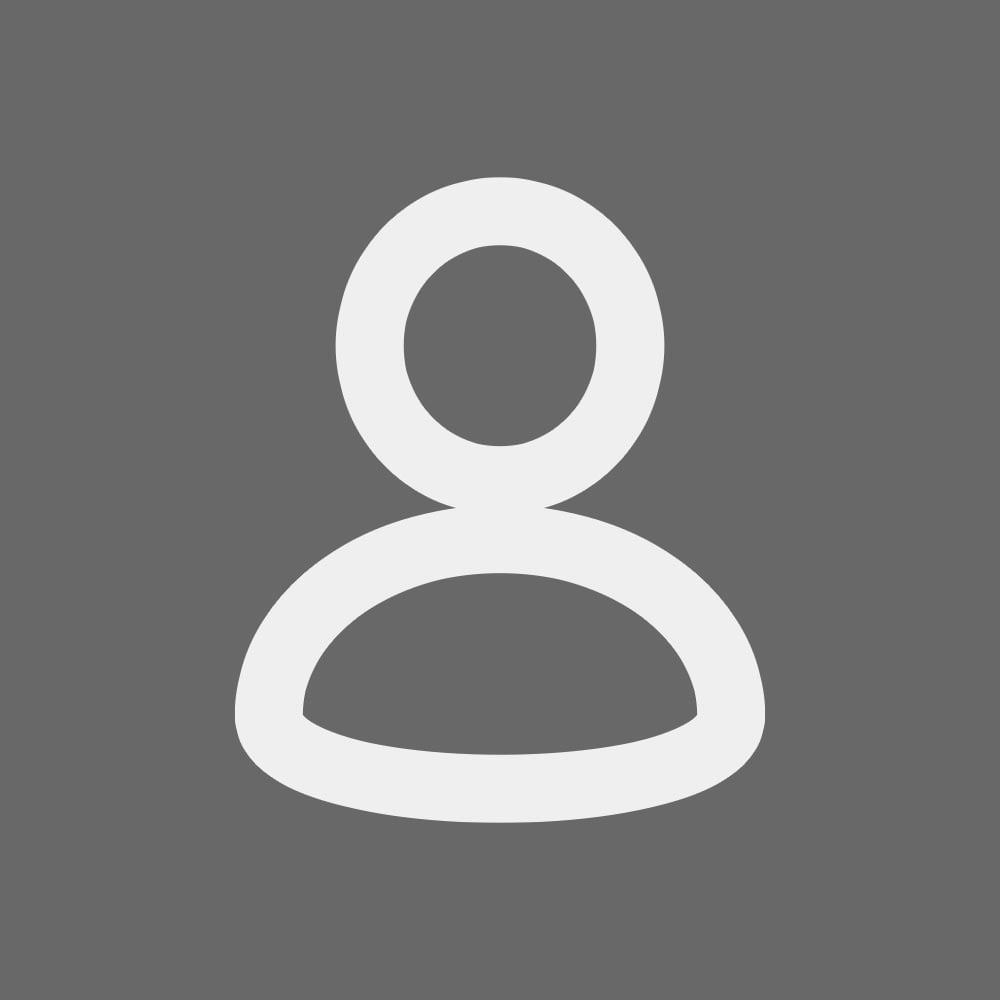
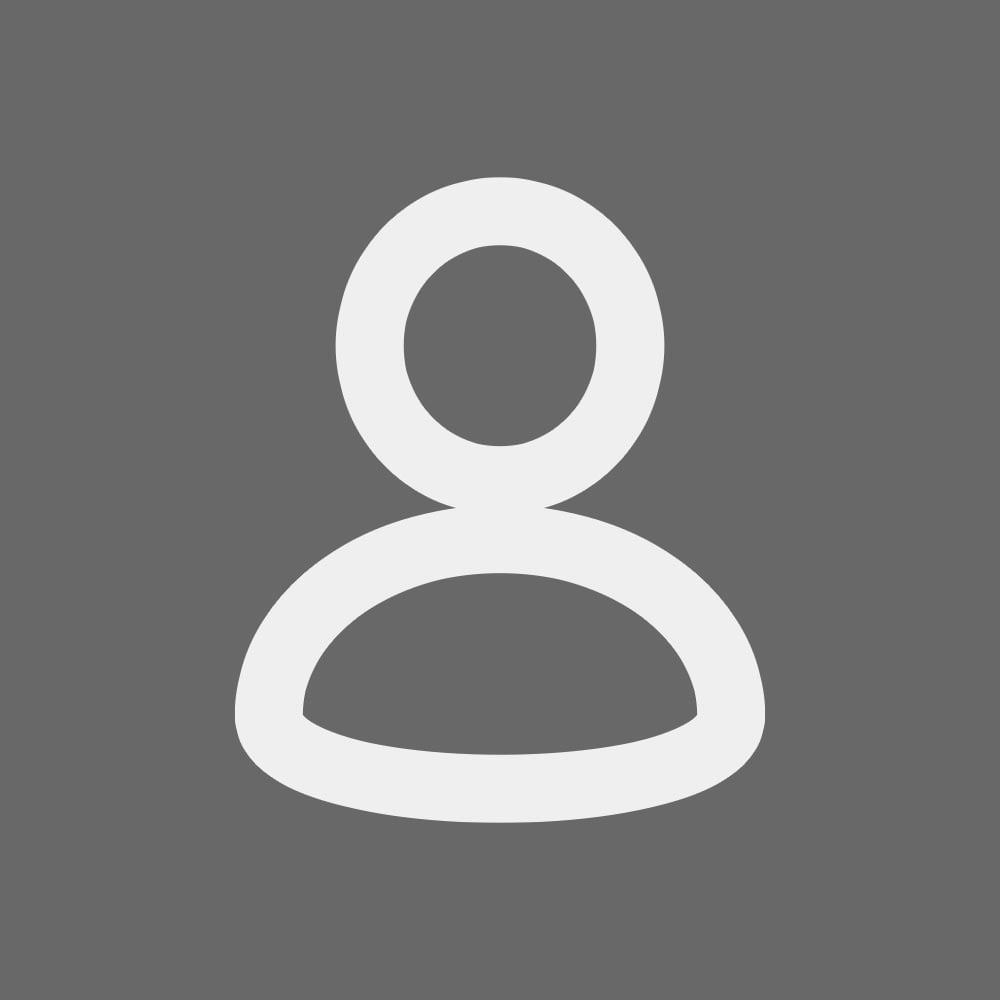
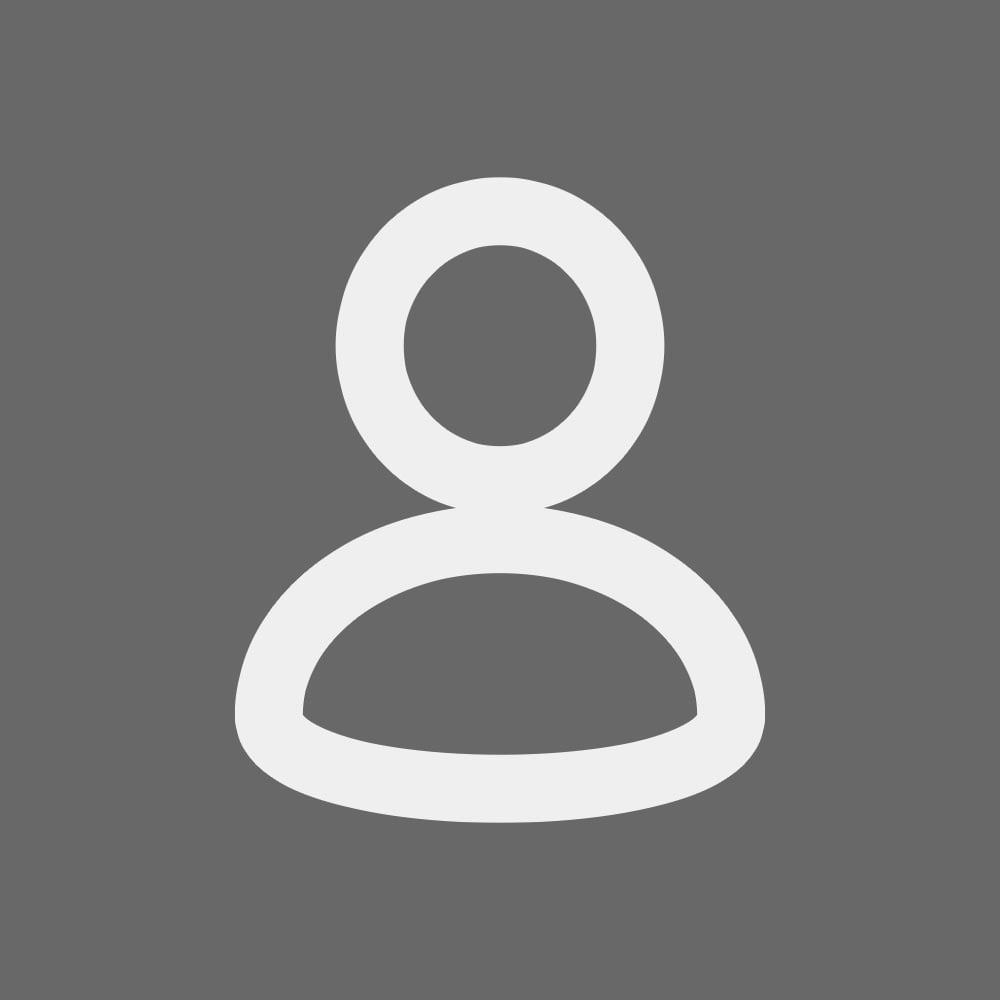
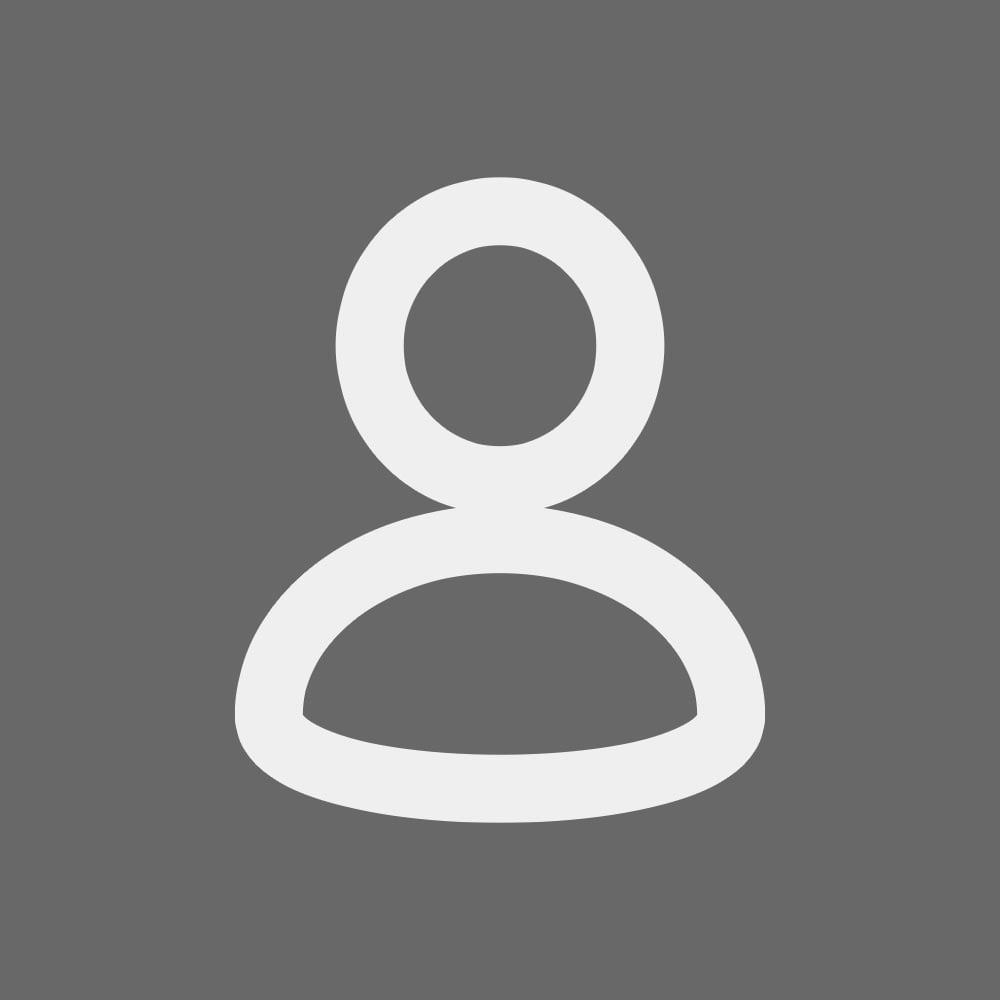
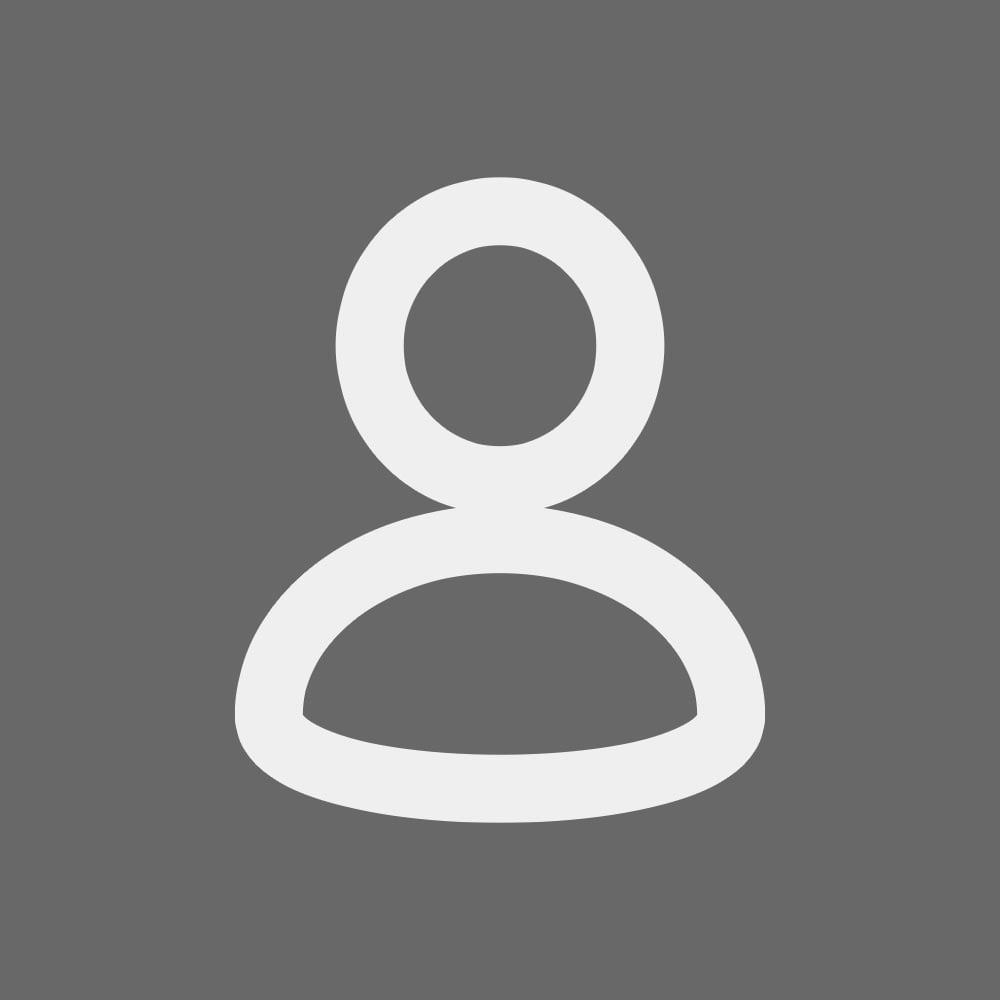
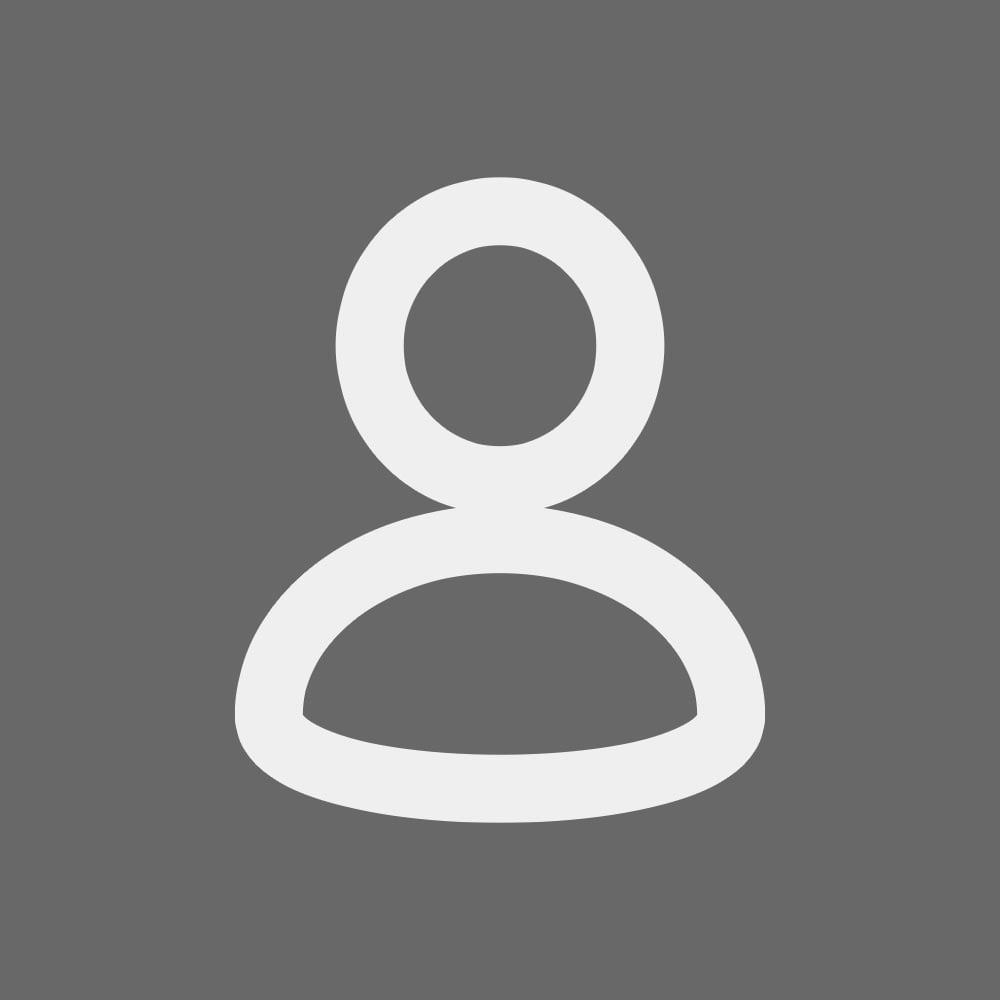
Tuhin Choudhury
Partners
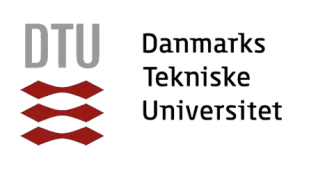
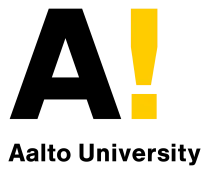
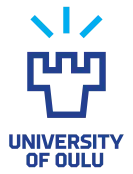
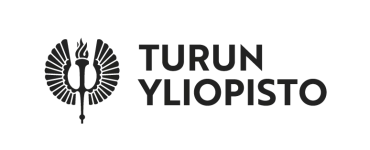
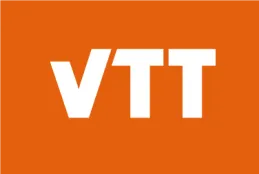
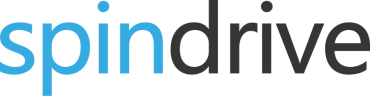
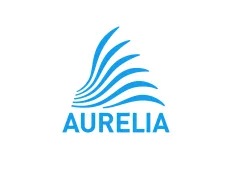
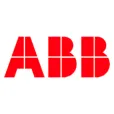
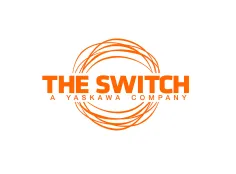
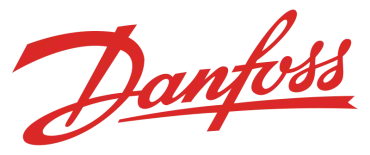