LUT-yliopistossa aiotaan tehdä painekoe Suomen suurimmalle metalli-3D-tulosteelle. Noin 300-kiloisen painesäiliön halkaisija on 900 millimetriä ja korkeus 1 600 millimetriä. Säiliö valmistettiin haponkestävästä ruostumattomasta teräksestä ja tulostettiin ANDRITZ Savonlinna Works Oy:n 3D-tulostuslaitteistolla.
Puhekielessä tulostusmenetelmä tunnetaan WAAM-lyhenteellä (Wire Arc Additive Manufacturing). Menetelmän toimintaperiaate on suorakerrostus, jonka energianlähteenä on valokaari (DED-Arc).
”Testattavan kappaleen rakenne on todella ainutlaatuinen. Tämä on Suomessa ja LUTissa ensimmäinen painekoe, joka tehdään WAAM-menetelmällä valmistetulle näin suurelle kappaleelle. Kyseessä on merkittävä suunnittelun, valmistuksen ja testauksen kokonaisuus myös maailmanlaajuisesti”, sanoo LUT-yliopiston hitsaustekniikan apulaisprofessori Tuomas Skriko.
LUTin teräsrakenne- ja hitsaustekniikan laboratoriot toteuttavat testauksen alkuvuonna 2023.
”On merkittävää, että voimme olla mukana määrittämässä painesäiliön materiaalista ja geometriasta määräytyvää suorituskykyä. Tämä on poikkeuksellinen testi myös meille, sillä edellinen vastaavan kokoluokan painekoe tehtiin parikymmentä vuotta sitten”, toteaa LUT-yliopiston teräsrakenteiden professori Timo Björk.
Tilaamalla uutiskirjeemme saat sähköpostiisi noin 1–2 kertaa kuukaudessa luettavaa tutkimuksestamme puhtaaseen energiaan, ilmaan ja veteen sekä kestävään liiketoimintaan liittyen.
Testauksessa saadaan tietoa valmistuksesta ja ominaisuuksista
3D-tulosteen testaus tehdään rikkoutumiseen asti. Toisin sanoen säiliöön kohdistetaan niin paljon painetta, että se hajoaa. Kappaleen kriittisiin kohteisiin kiinnitetään venymäliuskoja, joiden avulla voidaan seurata tulostetun materiaalin käyttäytymistä kuormituksen aikana. Testi kuvataan ja vauriot analysoidaan. Samasta materiaalierästä tulostettujen vetokoesauvojen avulla pystytään testaamaan rinnakkaiskokeissa perusaineen lujuusominaisuuksia.
Painesäiliön kansi 3D-skannattiin jo tulostusvaiheessa, ja koko säiliö 3D-skannataan vielä ennen painekoetta. Tuloksia verrataan ideaalimalliin, jotta mahdolliset valmistuksen aikaiset muodonmuutokset voidaan määrittää. Tulostusvaiheen lämpötilamittauksista saadaan tietoja jäähtymisnopeudesta ja sen luomista materiaaliominaisuuksista.
”Tuloksissa kiinnostaa se, kuinka mittatarkka WAAM-menetelmä on, sekä ennen kaikkea tämän kokoluokan tulostusten laatu ja materiaaliominaisuudet. Saamme paineastialle ja erikseen valmistetuille koekappaleille tehtävistä rikkomattomista ja rikkovista testeistä tarpeellista tietoa kappaleen lopullisista ominaisuuksista. Näin pystymme selvittämään, miten valmistusmenetelmää pystyisi painelaitteissa hyödyntämään kaupallisesti”, kertoo lisäävän valmistuksen päällikkö Santeri Varis, ANDRITZ Savonlinna Works Oy:stä.
Varis on LUT-alumni, joka teki vuonna 2020 diplomityönsä WAAM-menetelmästä.
Tulokset kiinnostavat myös kansainvälisesti
Painesäiliön tulostus ja testaus toteutetaan FAME-ekosysteemin (Finnish Additive Manufacturing Ecosystem), ANDRITZ Savonlinna Works Oy:n ja LUTin yhteistyönä. Lisäävän valmistuksen asemaa suomalaisissa yrityksissä edistävässä FAME-ekosysteemissä on mukana noin 40 keskeistä lisäävän valmistuksen yritystä ja sitä hyödyntävää yritystä. Säiliön suunnitteluun osallistui myös Elomatic, ja testauksen konsultointiin osallistuu Dekra.
”Painesäiliö keräsi valtavan määrän kansainvälistä huomiota, kun se oli esillä Frankfurtissa 3D-tulostuksen kansainvälisessä suurtapahtumassa Formnext 2022 -messuilla. Lisäksi kotimaassa säiliö oli nähtävillä Konepaja-, Nordic Welding Expo sekä 3D & New materials -messuilla, jossa se keräsi paljon yleisöä. Kiinnostus painetesteihin ja LUTin siitä tekemiin tutkimuksiin on valtavaa tulosten uutuusarvon takia”, sanoo ekosysteemijohtaja Eetu Holstein DIMECC Oy:stä.
Testien jälkeen säiliö kuljetetaan Vaasaan, Wärtsilän Sustainable Technology Hubissa sijaitsevaan avoimeen 3D-tulostuskeskukseen AM Campus 2.0:aan.
Lisätietoja:
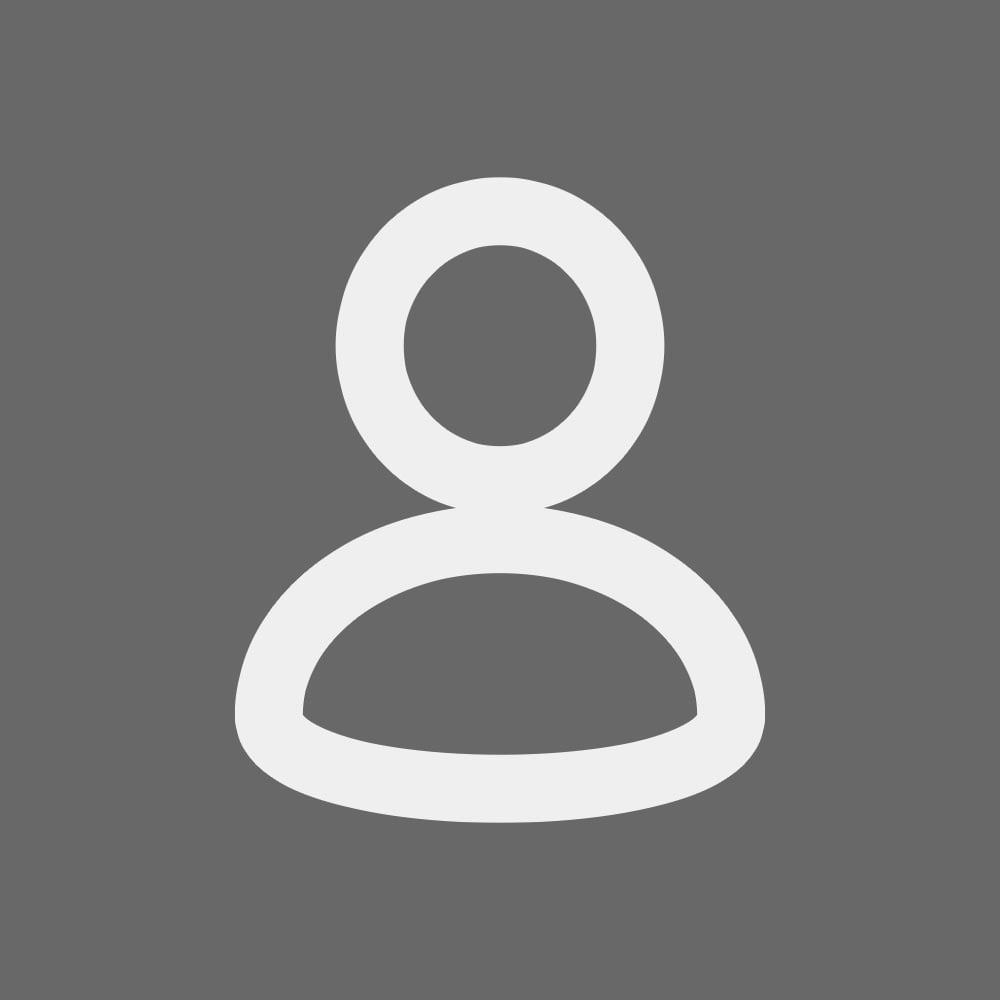
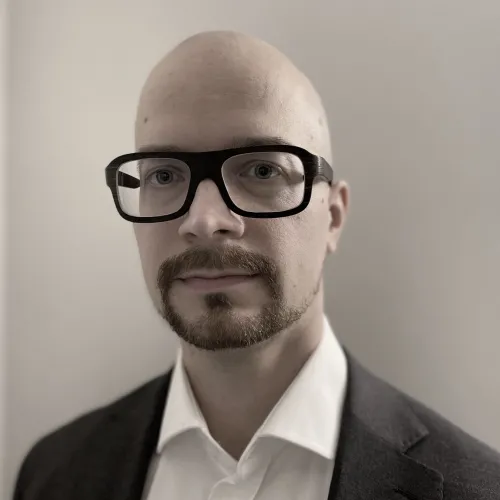
Tuomas Skriko
Eetu Holstein
Ekosysteemijohtaja, DIMECC Oy
+358 40 840 8660
eetu.holstein@dimecc.com